Nemetz Entsorgung und Transport AGStrong channel baling press for Nemetz Entsorgung Austria
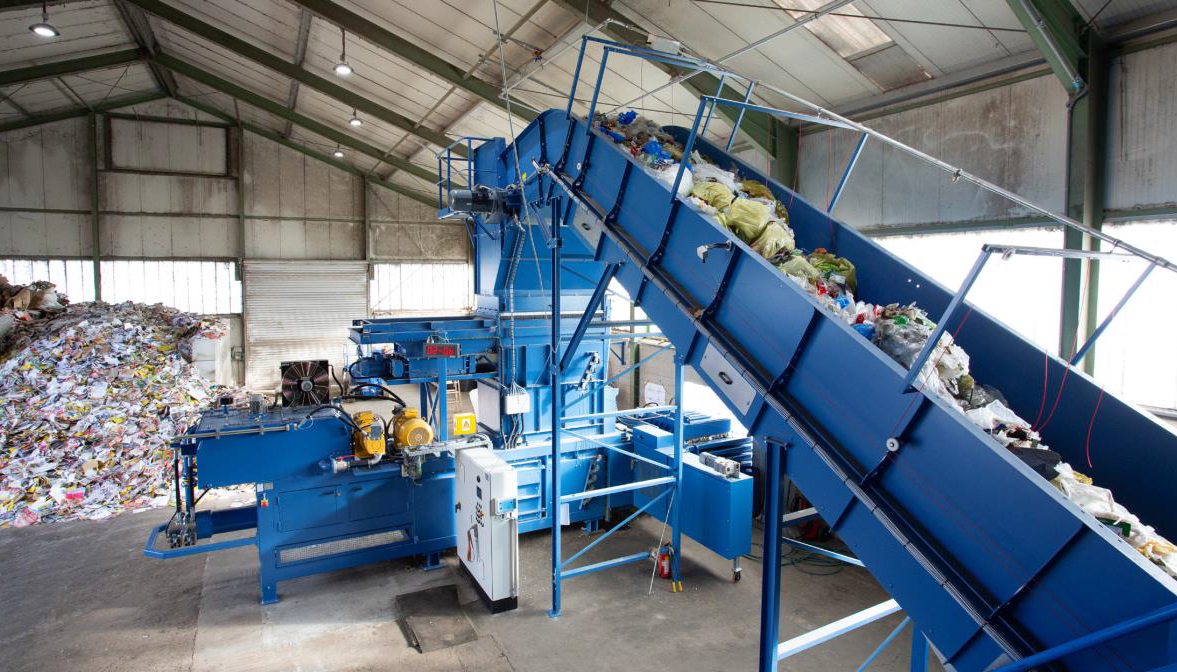
Nemetz Entsorgung und Transport AG
Founding Year
Headquarter
Industry
1915
Vienna, Austria
Waste disposal
- 7.000Accumulation points
- 4.000Customers
Thousands of tonnes of plastics, PET and AZV, aluminium and tinplate, as well as hollow containers are processed at Nemetz Entsorgung in Austria every year, . This is done fully automatically with our APK-ES120 channel baler with a pressing force of 1,350kN.
Environmental and climate protection through efficient disposal of all types of waste
The family-owned company with over 100 years of experience in waste disposal is the innovative partner of private individuals, companies and municipalities. Nemetz, with its future-proof waste disposal solutions for the protection of our environment and the climate, focuses on the responsible handling and use of all resources, from planning of all involved processes down to products and services.
The task: diversity, compaction, processing
The Nemetz company in Leopoldsdorf/Austria is recognised as a leading company in the field of waste management. Thousands of tonnes of mixed waste from the “Gelber Sack”, i.e. PET and recyclables, aluminium cans and further cardboard, tin plated and PE canisters, and hollow body waste are processed annually. The various waste materials are separated, collected, deposited onto the press plant conveyors and processed in the channel baling press. The objectives: maximum utilisation of trucks through high bale weights, compact and optimally stackable bales, fast change of materials and high productivity and economic efficiency of the plant.
The solution Austropressen automatic baler APK-ES: sustainable, efficient, versatile and prescient
The fully automatic Austropressen APK-ES120 channel baling press was selected as the solution to Nemetz requirements and the specific Nemetz variety of materials ‒ including 5-fold horizontal binding and 1,350 kN pressure force.
The APK-ES120 ensures energy- and resource-saving waste logistics. The channel baler will press the different materials into compact and stackable bales.
The APK ES-120 technical parameters:
Bales weighing up to 880 kg are produced under 1,350 kN pressure force and at a calculated 640 m³/h throughput, depending on material
Problem-free processing of mixed waste, pre-compacted cardboard, recyclables, PET, aluminium and tin plate, HD-PE canisters and hollow bodies
The energy requirement will be around 2.8 kW/h per cardboard bale with a bale weight of 700 kg and 1.1 m long
Exchangeable HARDOX base and side plates reduce wear and increase service life
A 2 x 45 kW drive with sensor-controlled switch-off in case there is no material infeed will guarantee efficient consumption of energy
Specially developed hydraulic units and an oil care system (cooling, heating, cleaning all-in-one) will ensure energy-saving operation and also serve to extend the service life of hydraulic equipment and fluid
Branded products installed: hydraulic equipment from Rexroth/Parker, electrical equipment from Siemens
Hardened piston rod
The patented cutting system will minimise jamming of materials, energy consumption and cutting tool wear
Ideally designed blades with optimum cutting angles and a clear-pressing system will ensure trouble-free and continuous operation
Clear-pressing system to clear jammed materials
Fully automatic 5-fold horizontal binding of the bales by the Austropressen DRILLFIX 2.0 system will save wire and ensure trouble-free operation. A wire insertion system ensures reliable and trouble-free binding of the bales.
Maximum safety based on key transfer to monitor doors
Automatic control system with pump switch-off, automatic press channel control and a user-friendly display
The APK ES-120 in numbers:
10 program settings for every material
Filling volume of 2.6 m³ with a fill opening of (l x w) 2 x 1.1 m and 4 m channel length
Machine weight: approx. 35,000 kg
Bale sizes from (w x h x l) 1,100 x 1,100 x 400 to 2,000 mm
Bale weights:
PET: 400 kg (1.2 m long), Carton: 700 kg (1.2 m long)
Foil: 680 kg (1.3 m long), Hollow bodies: 400 kg (1 m long)
Aluminium: 350 kg (1 m long), Tin plate and metal: 880 kg (1.3 m long)
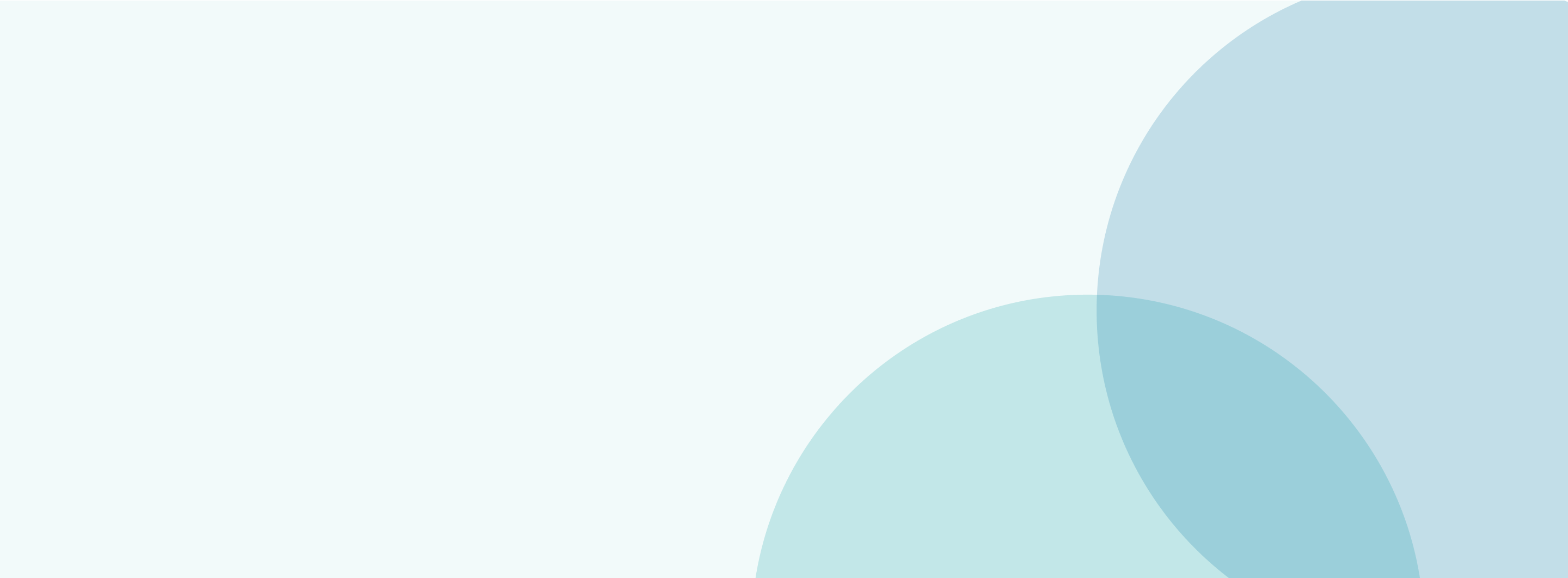
Take advantage of our experience.
Contact us and we will find the ideal solution for your company's use in a free consultation.