Penny DeutschlandReliable high performance for the central warehouse of PENNY Germany
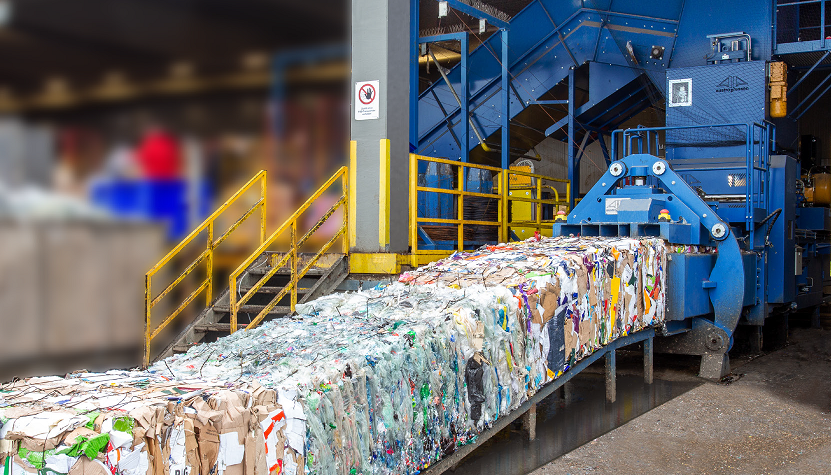
Penny Deutschland
Founding Year
Headquarter
Industry
1973
Köln, Germany
Retail trade
- 2.140Stores in Germany
- 30KEmployees
Penny's logistics centres are designed to use sustainable energy and recycle as many raw materials as possible. The APK-ES90 channel baling press from Austropressen makes a valuable contribution in the central warehouse in Eching/Germany.
Penny is one of the leading food discounters in Germany, boasting around 2,150 stores and currently 10 logistics centres. The topic of sustainability is high on the list of Penny’s priorities. And so also the topic of freshness: the stores are supplied with fresh fruit and vegetables daily; short delivery routes and regional products ensure that CO2 emissions are reduced.
The sustainability formula: avoid, reduce, optimize: The logistics centres are designed to operate using sustainable energy and to recycle as many raw materials as possible. The Austropressen contribution to recycling and waste management at the central warehouse in Eching/Germany is highly valuable here.
The task: sustainability, performance and economy
Around 12,000 tonnes of cardboard, PET and other recyclable waste are generated at the Eching site every year. Packaging materials from the surrounding markets are separated, collected, dumped onto the baling plant conveyors and processed in the channel baling press. These large volumes must be handled easily, fast and automatically – also considering conveyor technology and conservation of energy and resources. The objectives: speed, compression of a wide variety of materials into compact and stackable bales, maximum bale weights for optimal truck utilisation and system service life and reliability.
The solution APK-ES90: ecologically effective, powerful, reliable operation and future-oriented
The fully automatic Austropressen APK-ES90 channel baling press with its pressure force of 950 kN and with 5-fold vertical binding of the bales was selected to meet Penny’s requirements. The Austropressen chain belt conveyor with a length of around 13 m and its 5.5 kW drive is frequency converter driven for continuously variable speed.
The APK-ES90 technical parameters:
Bales weighing up to 650 kg, depending on material, are produced under 950 kN of pressure force and at a calculated 410 m³/h throughput
The system will effortlessly process PET, pre-compacted cardboard or recyclable waste at 20 sec. average cycle times
– Energy requirements at 1.8 to 3 kW/h per bale, depending on material, are lowExchangeable HARDOX base and side plates will reduce wear and increase service life
A 45 kW drive with sensor-controlled switch-off in case there is no material infeed also guarantee the efficient use of energy
Specially developed hydraulic units and an oil care system (cooling, heating and cleaning, all-in-one) ensure energy-efficient operation and serve to extend the service life of the hydraulic equipment and fluid
Installed branded products: hydraulic equipment by Rexroth/Parker, electrical equipment by Siemens
The patented cutting system will minimise jamming of material, energy consumption and cutting tool wear
Ideally designed knives with optimum cutting angles and a clear-pressing system will ensure uninterrupted trouble-free operation
Fully automatic 5-fold vertical bale binding using the Austropressen DRILLFIX 2.0 system will ensure smooth, trouble-free and safe operation with minimal use of wire
Maximum safety based on key transfer to monitor doors
State-of-the-art safety system for the conveyor belt: contactless safety device for operating staff, based on RFID transponders
Automatic control system with pump shut-down, automatic press channel control and user-friendly display
The APK-ES90 in numbers:
10 programme settings for every material
Bale sizes from (w x h x l) 1,100 x 750 x 400 to 2,000 mm
Filling volume of 1.55 m³ with a fill opening of (l x w) 1.7 x 1.1 m and 3 m channel length
Machine weight: approx. 24,000 kg
Bale weights & truck capacity utilization:
PET: 350 to 400 kg (1 - 1.2 m long) at 54 to 56 bales per 20 to 22 t truck
Carton: 500 to 650 kg (1.2 - 1.4 m long) at 43 to 46 bales per 25 to 26 t truck
Film: 400 kg (1 m long) at 60 bales per 24 to 26 t truck
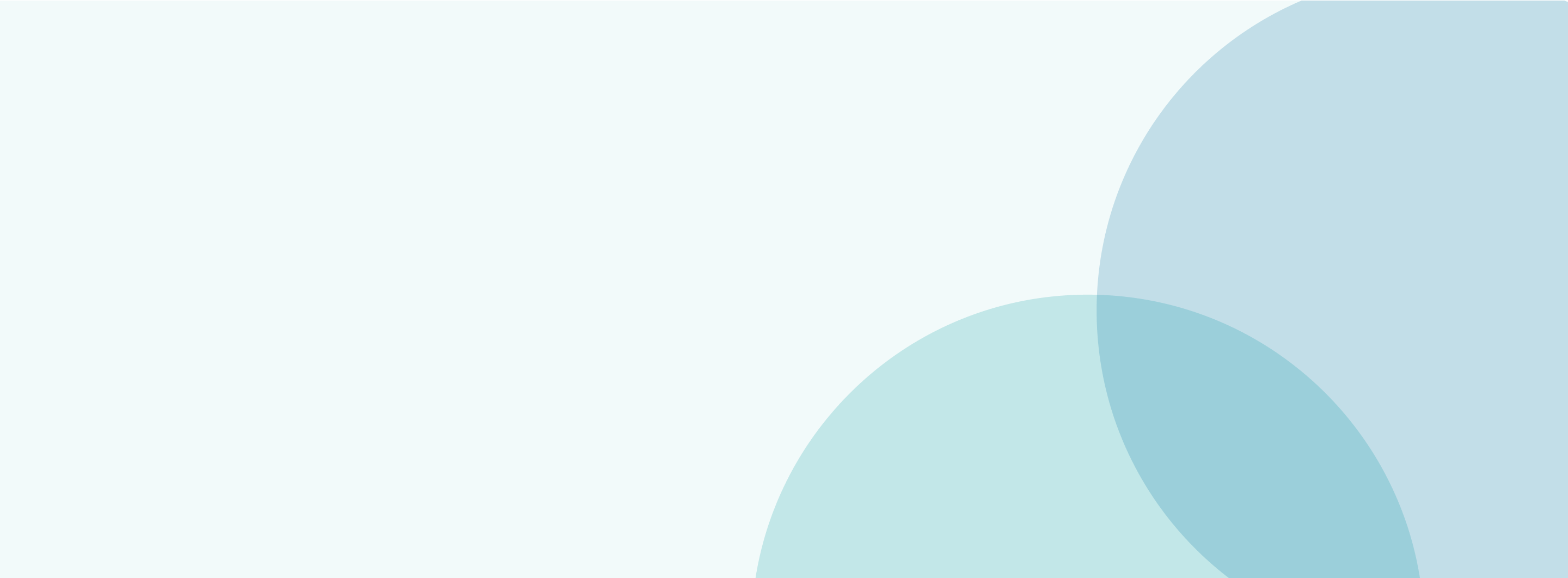
Take advantage of our experience.
Contact us and we will find the ideal solution for your company's use in a free consultation.