FCC Environment CEE GroupChannel baling press Austropressen APK-ES105 for waste disposal expert FCC
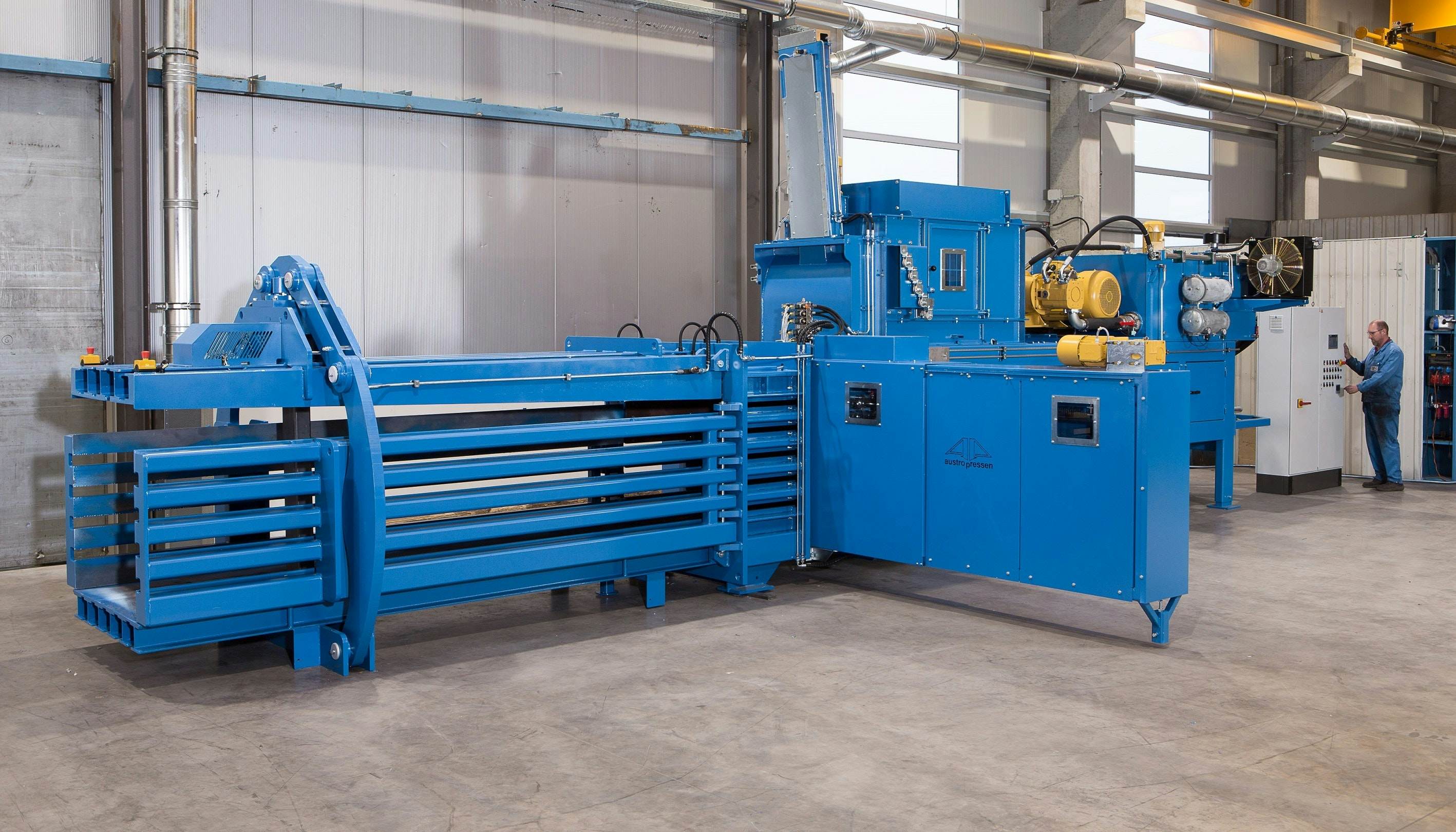
FCC Environment CEE Group
Founding Year
Headquarter
Industry
1988
Himberg, Austria
Recycling
- 7Countries present
- 4.400Employees
ENTSORGA, a subsidiary of the FCC Group, has been operating a landfill and recycling centre for household and commercial waste in Tainach for the past 30 years. An Austropressen APK-ES105 automatic baler with top-of-the-range equipment is now also in use at the site.
FCC Environment CEE is the largest environmental services group with main activities in waste management in Central and South Eastern Europe.
Top performance with unique features
FCC's Austrian subsidiary ENTSORGA has been operating a landfill and recycling centre in Tainach (Carinthia) for 30 years. An Austropressen APK-ES105 channel baling press with top equipment is now also in use there. Together with the technical manager, Hans-Jürgen Buch, the requirements were determined and implemented. The baler processes large quantities of residual and commercial waste. The bales are tied fully automatically with plastic or wire.
Austropressen APK-ES shows its power
At the FCC-ENTSORGA site in Tainach, residual, bulky and commercial waste are compacted. An average of 22t/h to 35t/h passes through the new channel baler at peak times.
The material is compacted fully automatically into bales measuring 1.1 x 1.1 x 1.4-2 metres. The bale weights are up to 2,000 kg for 1.9 m long bales of household waste and around 1,500 kg for 1.4 m long bales of sorted commercial waste.
Specifications and Equipment
Compression force 1050kN (in the event of material jam 1150 kN) and theoretical performance of 980 m³/h
Drive 2 x 45 kW and double pump operation for high energy efficiency
The fully automated binding system DRILLFIX can be feed with plastic or steel wire; 5-fold horizontal strapping with movable tying for easy access for servicing.
The completely newly-designed and patented cutting system decisively reduces the machines’ energy expenditure. This successfully minimises material jams and energy consumption per press cycle and wear and tear on the cutting tool is reduced.
In the event of overfilling or material jams the automatic fault removal (free press device) ensures that the press works reliably and continuously.
Sliding shield: The binding ports remain closed during the pressing process in order to prevent discharge of the residual material and liquids. The result is a clean working space for the operators and the adjoining plant. Value-protecting side effect: longer life expectancy (no pollution of the machine parts), faster servicing and reduced cleaning costs.
Cover caps for binding ports on the pressing plate remain closed during the pressing process; this prevents material jams and malfunctions and stoppages are almost excluded.
Changeable HADROX wear plates not only on the base, but also on the side walls, the pressing plate and in the channel. This results in optimum bale quality for every mixture of materials and at the same time significantly reduces wear and tear.
Automatic lubrication system for the pressing plate
Transfer of machine data via SmartView
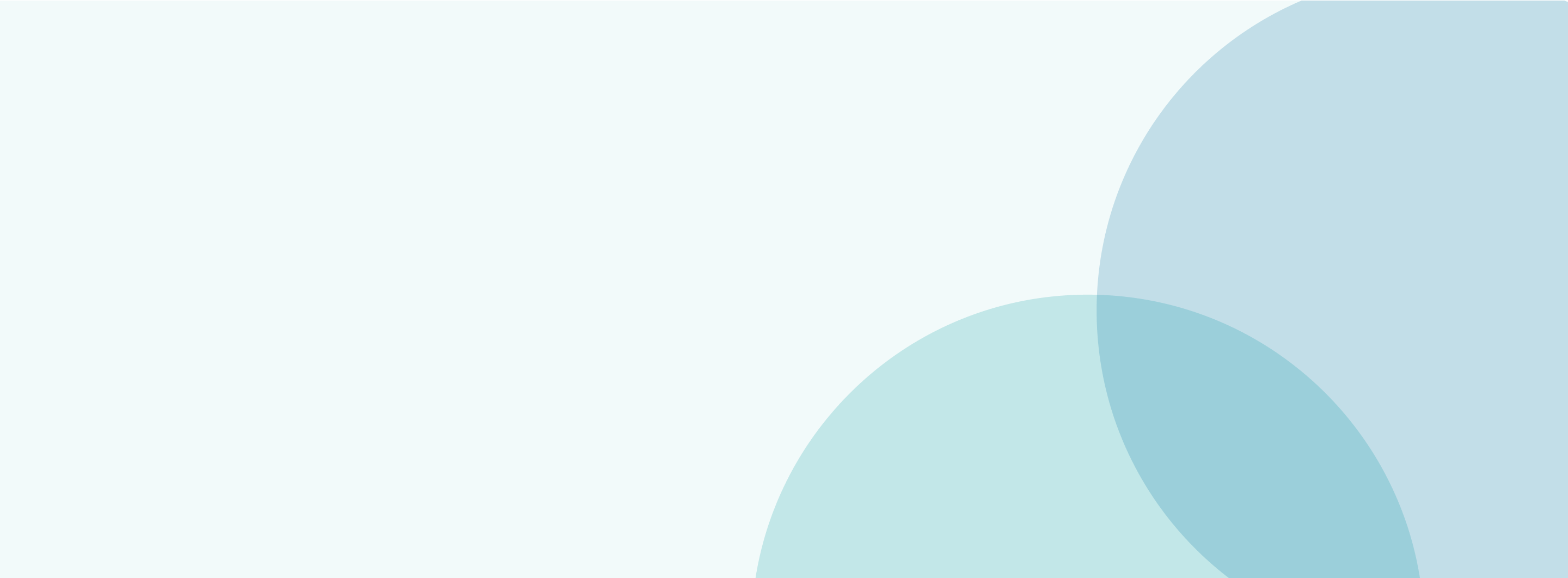
Take advantage of our experience.
Contact us and we will find the ideal solution for your company's use in a free consultation.