Zellinger GmbHSystematic disposal at Zellinger's waste management center
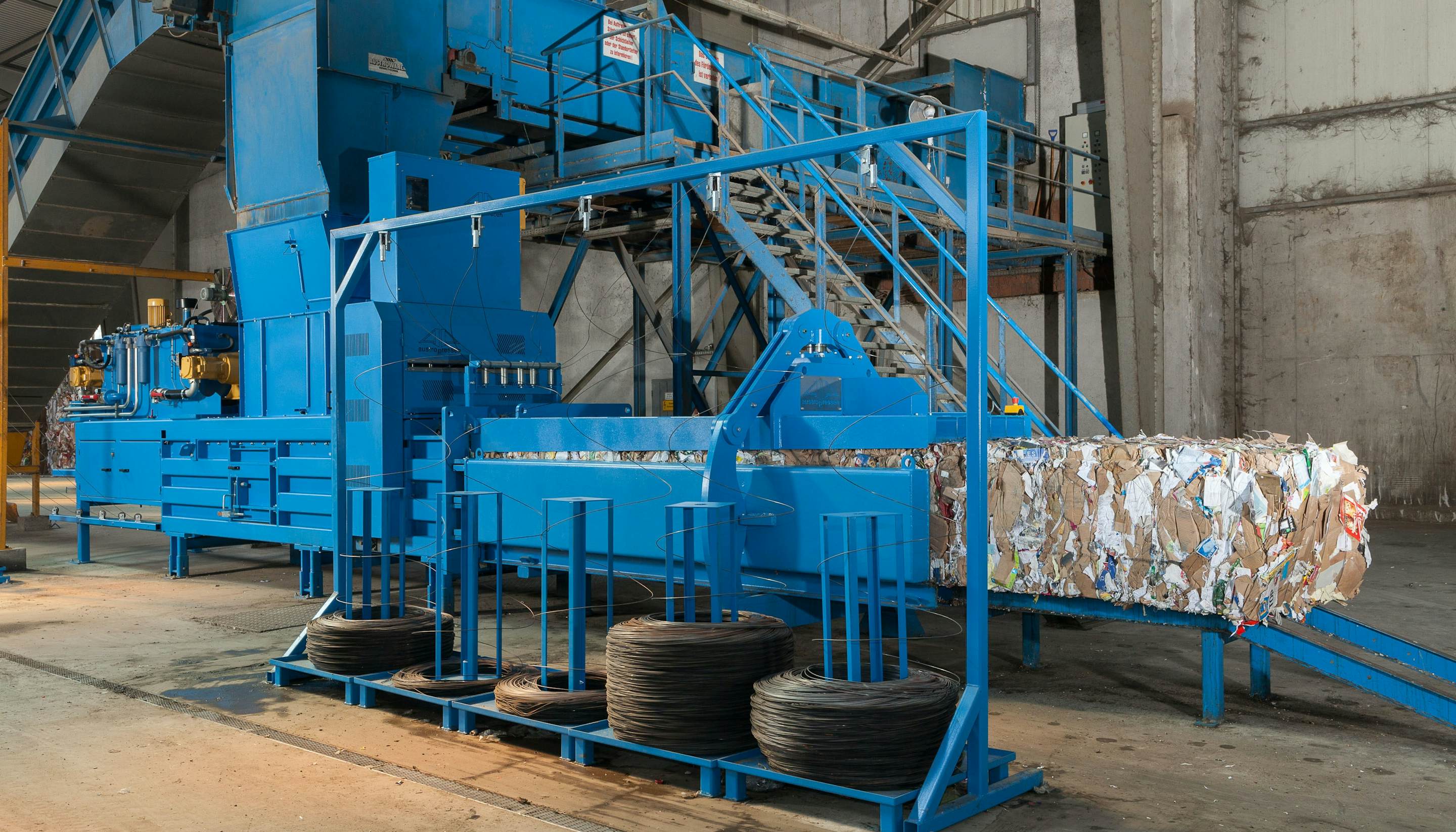
Zellinger GmbH
Founding Year
Headquarter
Industry
1955
Walding, Austria
Waste disposal
- 130Employees
- 4thGeneration
Systematic waste disposal. A newly commissioned Austropressen channel baling press APK-ES80 is ensuring efficient and cost-saving waste disposal logistics at the waste management centre at Zellinger GmbH in Austria.
Successful companies in the waste management and waste disposal sectors are relying on innovative strength and individual technical solutions. This equips them perfectly for the requirements that this important industrial sector places on them, in both municipal and commercial areas.
Stackable, transportable bales for the optimum loading of trucks, pressing of different types of waste, savings on energy and binding wire. This summarises the requirements of Zellinger GmbH in Herzogsdorf / Upper Austria, when they began their cooperation with Austropressen-Roither Maschinenbau GmbH. After a development and production time of a few months the fully automatic channel baling press APK-ES80-1700 successfully began its operation at Zellinger’s waste management centre.
Customer's requirements: excellent energy and material efficiency
Peter Zellinger and Jürgen Humer sketched the requirement profile of Zellinger GmbH, one of Upper Austria’s leading waste management and disposal companies, as follows: “We were looking for a press that can be adjusted perfectly to our waste processing situation and that achieves excellent results with regard to energy and material efficiency.”
Zellinger operates a waste management centre in which different systems, such as a splitting system for commercial waste and wood or a sorting system for plastic waste, are in use. After processing, this waste is pressed into transportable bales – depending on the material (from cardboard to PET bottles, foils, cans and through to car bumpers) and delivered to the various recycling or disposal processes. A detailed catalogue of measures and a project plan were produced in order to achieve these specific, transportable bales as required for different materials.
An automatic channel baling press with many advantages
Engineer Franz Roither and his team at Austropressen chose to install the channel baling press APK-ES80-1700. It not only fulfils all requirements but also offers decisive advantages: a lot of power, low consumption of energy and wire, precision and reliability.
The impressive parameters of the Austropressen APK-ES80
Pressure force: 800 kN, specific pressure: 99 N/cm², bale sizes: 720 x 1100 x 400-2000 mm, channel length: 4000 mm, loading volume: 1.80 m³, loading aperture: 1060 x 1700 mm, power: 2x45 kW, theoretical power: 540 m³/h, weight: 21,500 kg, dimensions: 11500 x 2200 x 3500 mm, hydraulic equipment: Rexroth, display: Siemens Touch Panel.
Energy efficiency is secured by two, separate hydraulic pumps and a specialist control system on the APK channel baling press. At low filling quantities – up to 180 m³/h – only one hydraulic pump runs. If the feed with waste material increases to up to 360 m³/h then a further light barrier reacts and the second pump automatically activates. This intelligent switching means that the full power is only called up if needed, which results in a power saving of up to 40% (based on a 2 x 45 kW press).
The machine offers maximum safety during operation but also during maintenance with the new, integrated key transfer system. Maintenance and service doors are monitored mechanically and efficiently secured by means of key transfer.
The fully automatic binding mechanism for bales with a maximum weight of up to 600 kg ensures both the desired reliability and optimised material use. The Drillfix binding unit works at the highest level and guarantees the precise binding of highly compressed bales. The wire feed at the top and bottom is a decisive quality improvement and is used to achieve automatic free space for the binding slots. In the event of overfilling, the free press device presses the surplus material away from the cutting edge and thus allows the press to work reliably without malfunction.
The channel regulation can be adjusted on the display for different materials in order to produce optimum bale quality. A long press channel for greater compression and the efficient binding system, which saves up to 1 m of wire per bale, are further features included in the channel baling press APK-ES80-1700.
Thus, for example, approximately 15 cardboard bales (bale size 1.10 x 0.75 x 1.80 m) can be produced per hour with this automatic channel baling press with bale weights of approximately 850 kg. This results in a production rate of approximately 13,000 kg/hour or one complete bale every 4 minutes.
This automatic baler can also be used for the highly efficient processing of PET bottles. Bale weights are approximately 260 kg for non-perforated bottles without tops (creating a bale size of 1.10 x 0.75 x 0.80 m). For perforated PET bottles (bale size of 1.10 x 0.75 x 1.00 m) the bale weights are approximately 350 kg. Wooden fruit boxes can also be quickly pressed into bales (bale sizes of 1.10 x 0.75 x 1.20 m). The bale weights here are approximately 320 kg.
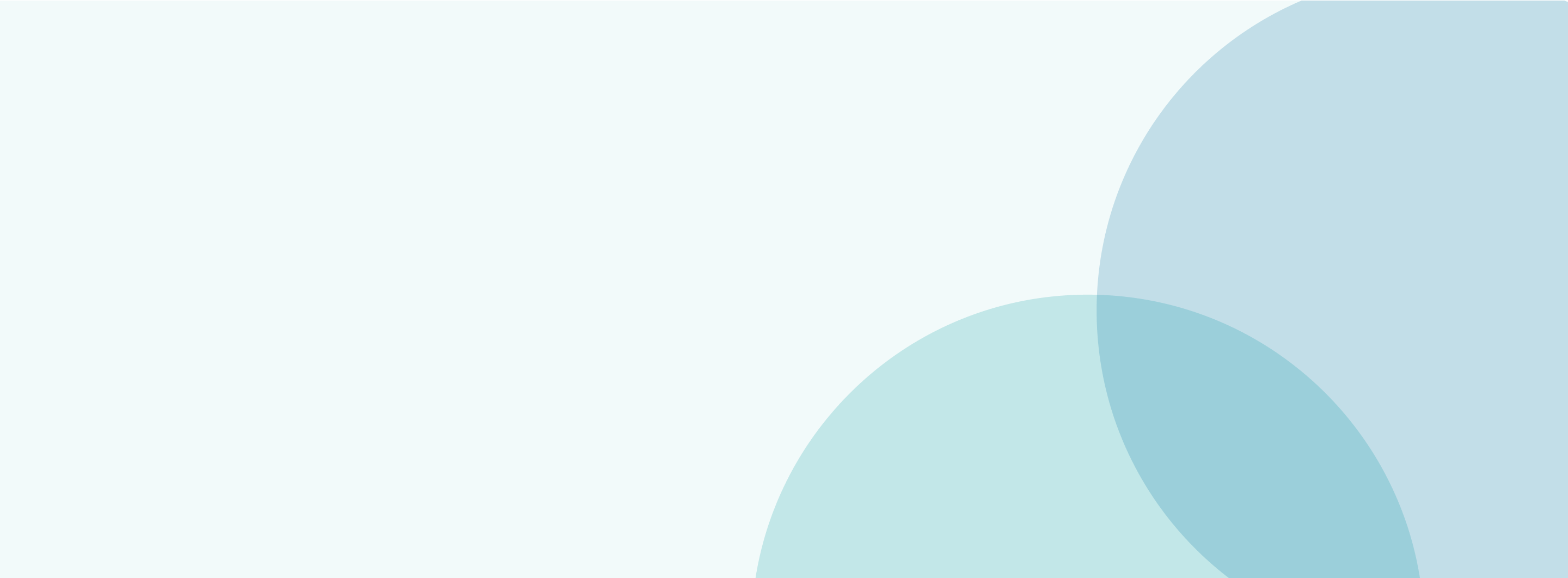
Take advantage of our experience.
Contact us and we will find the ideal solution for your company's use in a free consultation.